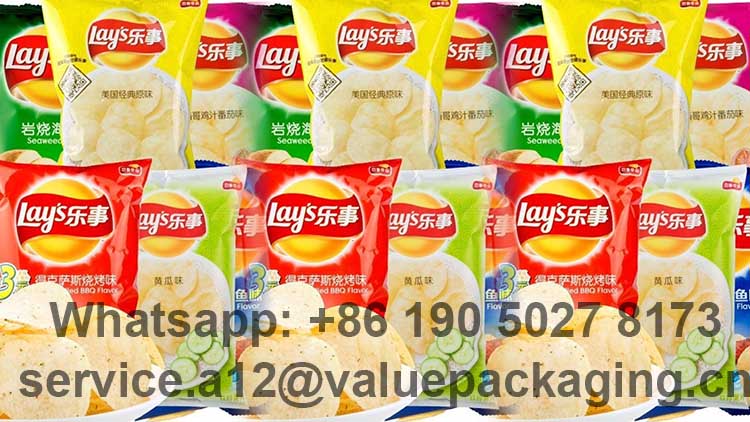
Pillow pouches are a large part of the packs for potato chips in the current market. The pillow pouches can easily hold extra products, and at the same time, present better display when they stand on the goods shelves. As a porpuct consideration, VMPET film is widely applied in the package for various potato chips nitrogen flushed pouch. Based on a flexible combination of various polymer film materials, the foil materials provide excellent barrier properties, protecting the potato chips from air, moisture, and light. Moreover, a creative artwork design, including all the information for branding and sale, can be printed on both sides of the pillow pouch, making the final package more attractive to consumers.
Located in Qingdao, China, we are a well-known flexible converter that uses the best film materials available on the market.
- fossil chemical polymer films
- Aluminum foil metal sheet
- vacuum metalized film materials
- Ceramic film substrates
- plant-based biopolymer materials
- biodegradable film materials
- compostable substrate films
- Fully recyclable substrate films
We are devoted to creating story-telling for potato chip pouches that increase product sales and establish a good brand image.
In this post, we will analyze the exact foil materials of this 75-gram potato chip pillow pouch, hoping it could serve as a reference for your products.
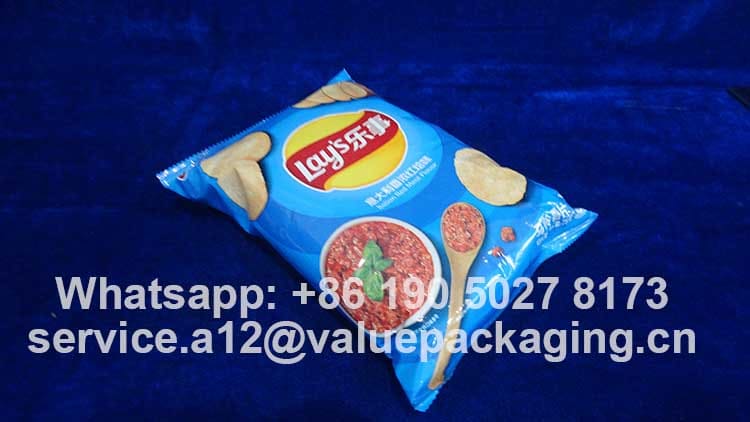
Ok, let’s get into the details of this potato chops pillow pouch.
Packaging Foil Materials
The figure below shows the composition structure of this laminated foil material used to convert this potato chip pillow pouch. It’s made of triplex layers for PET/VMPET/LDPE material film.
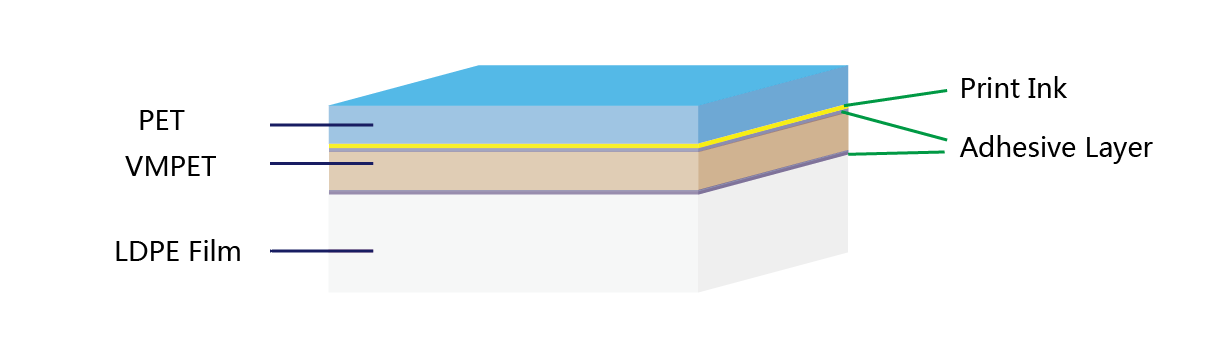
The outside PET film 12 microns working as the print substrate film, PA film 15 microns working as the middle supportive layer, and finally, the LDPE film working as the inner sealing layer. The thickness LDPE film should be adjusted to suit the requirements of 1800ml detergent liquids.
Next, let’s get into a deeper understanding of each substrate film material.
PET Film
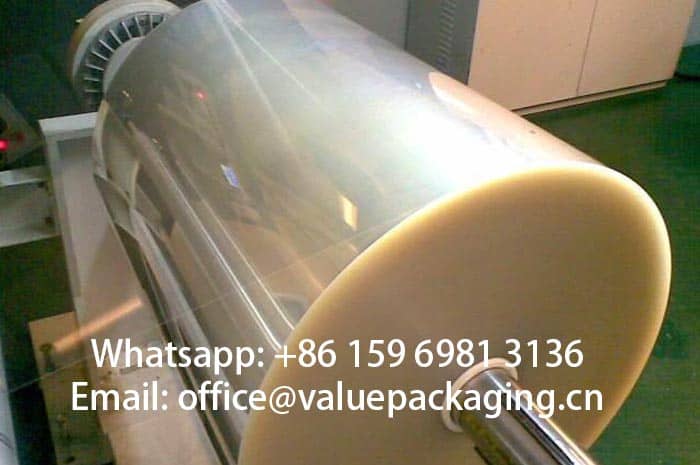
PET Film, is one of the most commonly used printing substrates in flexible packaging sachets. With great optical clarity, high gloss, good chemical resistance, stable mechanical strength, excellent dimensional stability, and great printability, it can present the customer artwork print in great quality, and also provide great mechanical strength to the final package.
The most commonly used thickness of PET film applied in the flexible packaging industry is 12 microns, which equals 0.48 gauge. So whenever you see PET12 or 0.48 g PET, you will know they mean the same thing.
VMPET Film
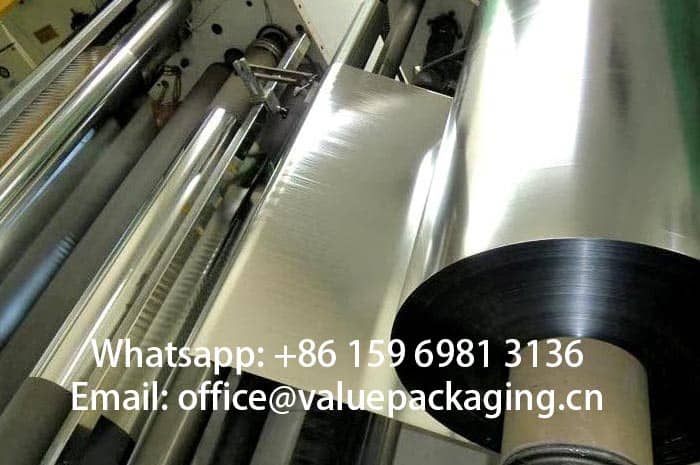
VMPET film is short for vacuum metalized polyester film, which is achieved under vacuum conditions to deposit a thin layer of aluminum atoms onto the surface of a PET (polyester) film substrate. And finally, realize a bright metallic film that is widely used in flexible packaging and standup pouch packages.
VMPET film has better sunlight shield properties. Sunlight shield property means the package with VMPET film can well protect the inside products against sunlight, like potato chips, liquid detergent, cookies, instant noodles, etc. VMPET film is the best solution for these product’s packaging. Also, VMPET film is so widely used in standup pouch packages that it has a high barrier property at quite lower costs than aluminum foil.
LDPE Film
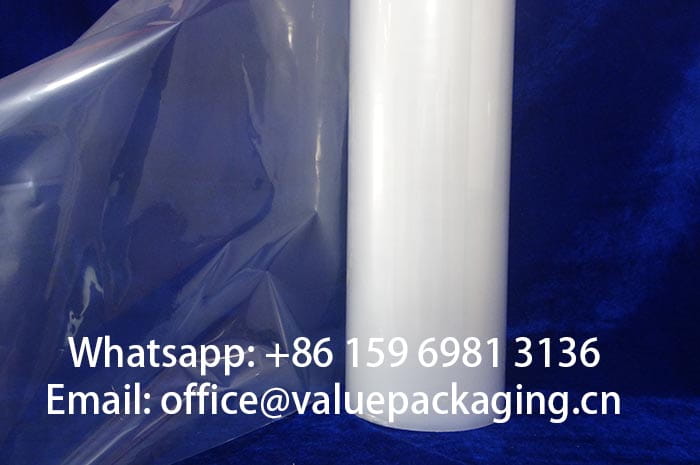
LDPE means low-density polyethylene film, which is the most commonly used inner sealing film for multi-layer flexible packaging in various applications. It can provide enough sealing strength and airtight properties for the final packages.
LDPE is lightweight, easy to fabricate, and has good chemical and impact resistance.
LDPE is recyclable and reusable, making it a popular alternative to traditional plastic.
LDPE is nontoxic, non-contaminating, and has a high degree of break resistance.
These 3 layers are bonded together into a finished laminated foil material under the dry lamination or solvent-free lamination process. Usually, we describe the finished laminate as PET/VMPET/LDPE foil.
Thickness
As you can see from the below picture, the overall thickness of this pillow pouch is 0.122 mm, which equals 122 microns for this laminated foil.
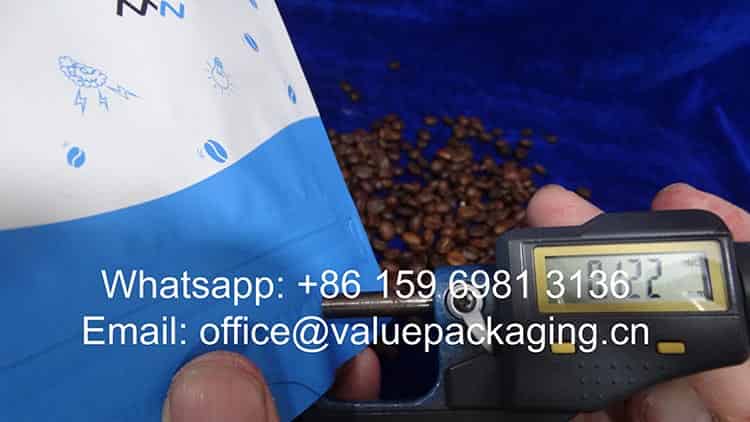
So, how does this foil structure perform when it is intended for potato chips? Will it break during the transit?
Great Standup Effect
Through the below picture, you may learn the potato chips pillow pouch effect when 75 grams of potato chips are filled into a pillow pouch based on this laminated foil PET/VMPET/LDPE.
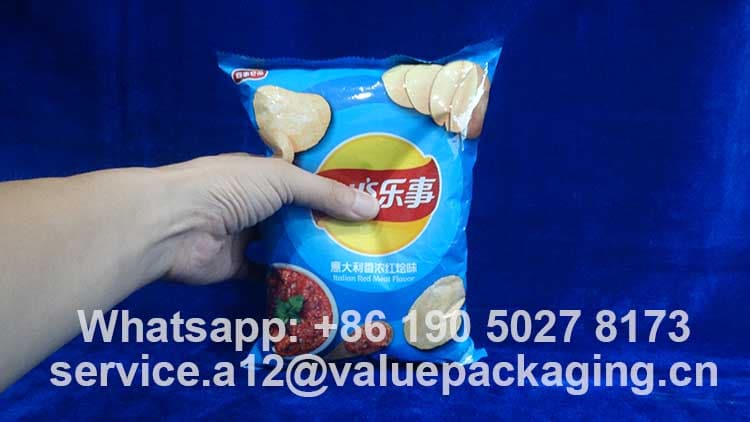
Mechanical Property
The pillow pouch package will protect the potato chip product during filling, transit, and distribution. Under the emergency circumstances of unexpected shock in delivery or packages falling off the goods shelf, the nitrogen-flushed pouch can better protect the product from damage.
We put the mechanical properties of this 75-gram potato chip pillow pouch our top priority in our manufacturing plant. Serious measures are taken in our QC system, to assure each order is finalized with the expected result.
Here’s a video to help you better understand why potato chip packaging needs VMPET film.
Barrier Performance
This reinforced laminated foil is achieved with great mechanical strength, with some standard items as below.
- Tensile Strength
- Sealing Strength
- Anti-puncture Strength
- Burst Impact Strength
- Anti-pressure Property
The above tests are performed against each order, on customer requirements, and you may check the exact values of this foil material in the Technical Date Sheet part of this post.
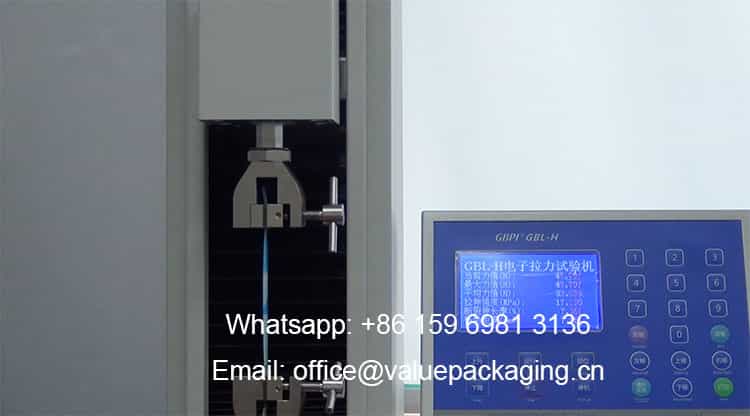
With the mocon O2/H2O/CO2 permeation tester equipped in our laboratory, we are able to keep a closer eye on the barrier performance of each laminate foil produced in our manufacturing plant.
Through the below table, you can easily find out the typical values of moisture vapor transmission rate and oxygen transmission rate of common substrate film materials.
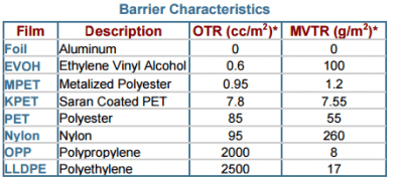
To ensure great protection of the potato chip from oxygen, and moisture, usually, a layer of metalized polyester film or aluminum foil sheet is applied in the foil structure, with some common foil structures as below.
- VMPET/LDPE
- BOPP/VMPET/LDPE
- MatteBOPP/VMPET/LDPE
This foil material proves to be working well for dry nuts and snack products distributed around the country.
Technical Data Sheet of 75 grams potato chips pillow pouch
Here, we attach the specification sheet of this 75-gram potato chips pillow pouch sahcet based on foil laminate PET/VMPET/LDPE.
More tests are included in this specification sheet with items available listed as below.
- Yield (grams per square meter)
- Tensile Strength (Mpa)
- Elongation Rate (%)
- Coefficient of friction, short as COF
- Solvents Left (mg/m2 )
- Sealing Strength (N/15mm)
- Sealing Conditions
- Bond Strength (N/15mm)
- Burst Strength (J)
- Anti-Puncture ability (N)
- Drop Test Ability (cm)
- Anti-pressure ability (kgs)
- Water Vapor Transmission Rate (g/m2/24hr)
- Oxygen Transmission Rate (cc/m2/24hr)
If you want to get a further understanding of this PET/VMPET/LDPE laminated foil, you may just read it here.
More Sustainable Materials Options
In recent years, along with the increasing burden of fossil-chemical polymer materials discarded into our environment, there has been an increasing focus on using more sustainable materials. there is an unprecedented demand for sustainable packages which leads to a more eco-friendly activity of the business. Upon the recent investigation of the nut market, more and more consumers are more likely to purchase a product that acts toward environmental sustainability.
Compostable Packaging Materials
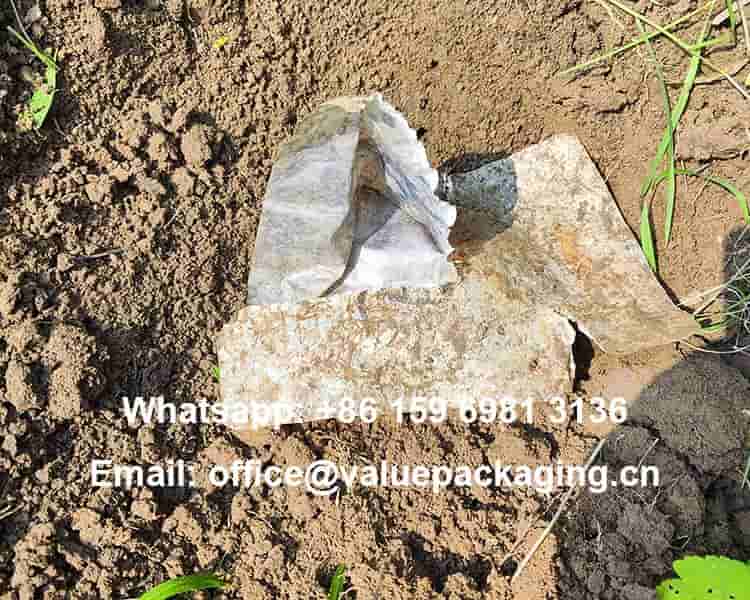
For example, Kraft Paper is already a relatively sustainable option as it is made from renewable wood pulp. In addition,the compostable packages are based on plant-based fibers like cellulose, or bio-mass like corn starch, cassava, or sugarcane. The resins derived from these resources are usually named bio-polymer, which can break down into inorganic elements under the functions of algae, bacteria, and other microorganisms.
At present, we have developed several compostable foil materials that can be intended for nuts, with list as below.
- Cellulose/Metallized Cellulose/PLA+PBAT Film
- Cellulose/Metallized Cellulose/PBS Film
Fully Recyclable Mono Materials
Compared with the high cost of compostable foil materials, fully recyclable materials sachets, and rolls are flooding the market for lightweight product packages in the market at much lower prices. Mono materials packages mean each layer of the multi-layer foil is made of the same resin, which can be easily processed in the human recycling system and reused for other applications. This recyclable materials sachet largely reduces the rate of plastic polymer film packages ending in landfills.
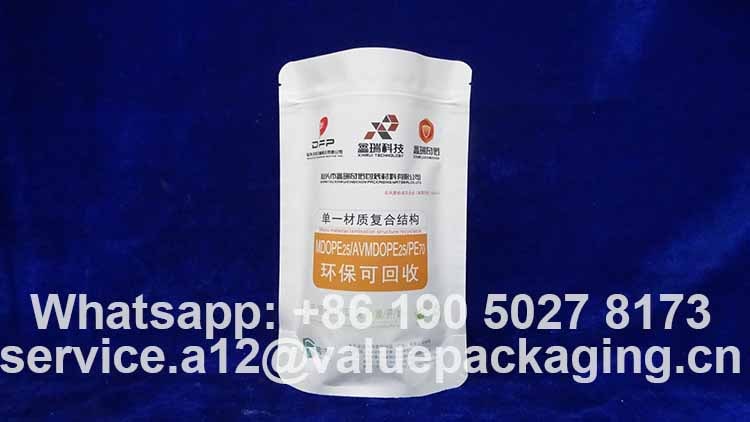
Nowadays, we have developed some standup pouches based on single resin film materials, that can be found in good application for roasted almond products.
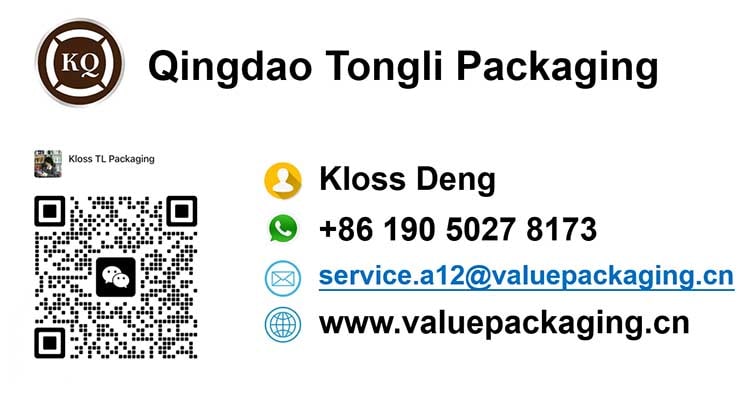