Description
1 Introduce
This admirable 180g bag is produced for yogurt, and this package is well able to present exceptional quality packages for the products and works as great protection in the filling, transport, and distribution process.
Here we will analyze this amazing yogurt bag further and hope you will get a fantastic product package.
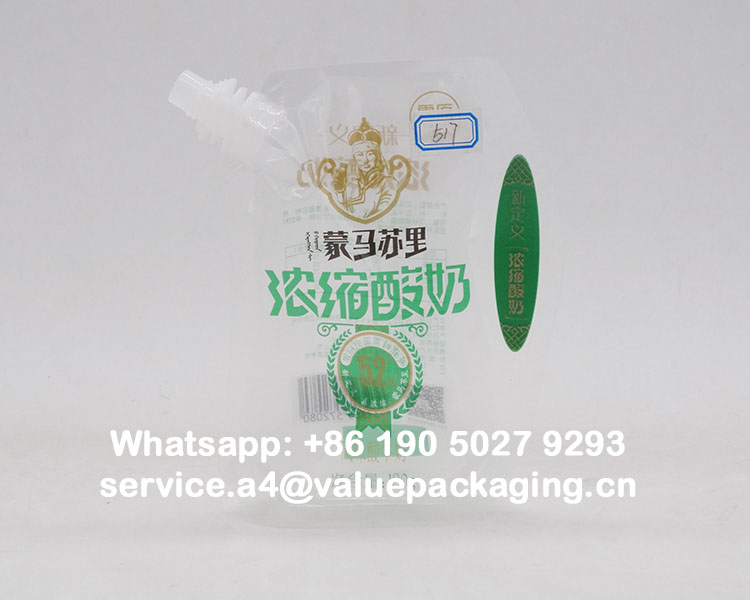
517-clear-standup-pouch-package-for-yoghourt
Watch the video for this 180g aluminum foil standup yogurt bag
2 Foil Materials
This foil material is a reinforced structure with excellent properties for yogurt bag packages. The foil structure is PET12/LDPE90, with a graphic as below.
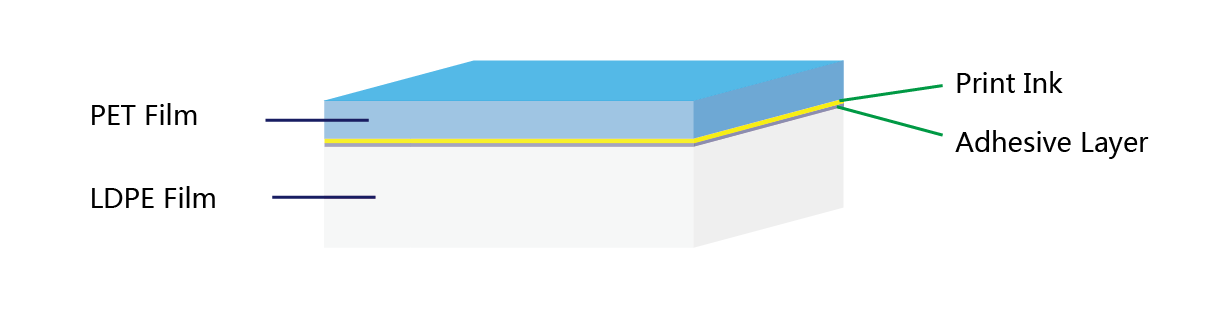
PET-ink-adhesive-LDPE-film
Let’s first get a further understanding of each substrate layer material.
PET12 is one of the most commonly used printing substrates in flexible packaging pouches. With great optical clarity, high gloss, good chemical resistance, stable mechanical strength, excellent dimensional stability, and great printability, it can present the customer artwork print in great quality, and also provide great mechanical strength to the final package.
LDPE means low-density polyethylene film, which is the most used inner sealing layer for yogurt bags. LDPE is also lightweight, easy to fabricate, and has good chemical and impact resistance. LDPE is recyclable and reusable, making it a popular alternative to traditional plastic. LDPE is nontoxic, non-contaminating, and has a high degree of break resistance. Most importantly, LDPE membrane can be modified against the requirement of specific products, and finalize the package with great seal strength and protection. The thickness of the LDPE membrane will be decided against particular.
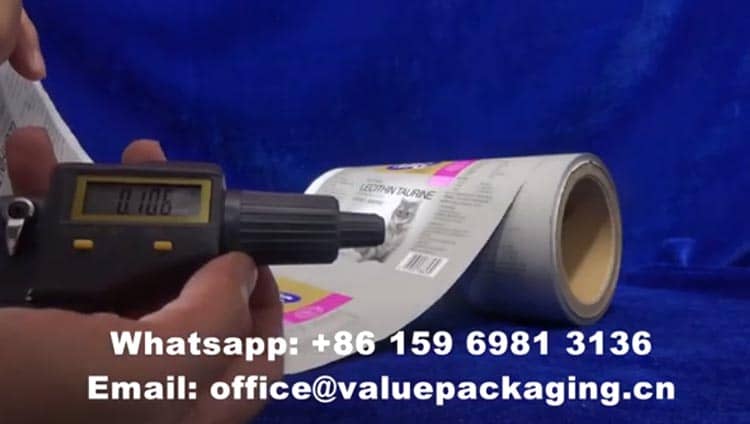
thickness-pet-ldpe-180g-yogurt-bag
The final thickness for this foil laminate should be 105 microns, with a tolerance of +-5%. and the toughness will be enough to present a good standing effect for finished bags.
You may read here on our company website to get a deeper understanding of PET12/LDPE Foil Laminate and see how it can help you to decide the ideal packages.
https://www.valuepackaging.cn/foil-structures/plastic-foil-laminates/pet-ldpe-foil-materials/
3 Properties and Quality Assurance
3.1 Exquisite print quality
The artwork is achieved in gravure printing on our rotogravure print press which can print up to a maximum of 10 colors. With advanced print techniques and a print defects inspection system, we are now outputting fantastic print effects for the customers’ artwork.
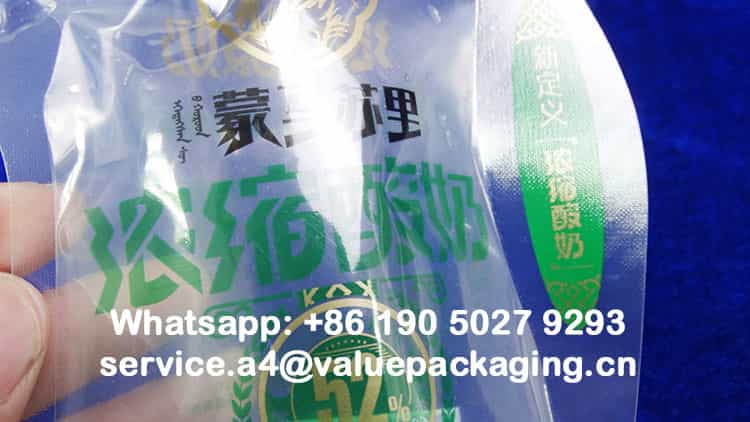
517-clear-standup-pouch-package-for-yoghourt4
In our manufacturing plant, we take serious measures to ensure high color fidelity and consistency for repeated printed orders. Here is a basic introduction.
a. Color Analyzer
This color analyzer is one of the auxiliary tools in our system to achieve the highest standard for color fidelity. The eXact Advanced doesn’t just validate the color of CMYK and spot color inks, it can simultaneously measure four M modes to visualize the spectral reflectance of a substrate or ink, measure the concentration of a specific ink, and measure the difference of a substrate or ink over white and over black.
b. Pantone Color Code
The Pantone color guide would be very helpful in locating a specific color for the spring service supplier and the customers, especially if there is a large area printed in a single Pantone color. For many Pantone colors, the accuracy may be influenced by the printer, paper substrate, and environmental factors when it is printed onto physical photo paper. We will locate the Pantone Color Code with the customers in their artwork design before the order is put into production.
c. Physical Printed On Photo Paper
Computer files such as JPG, PDF, PSD, AI, etc can not be taken as the guide to determine the color in print produce, as they present the colors through electronic screening devices. Different electronic screens may be set in different parameters by the various manufacturers, which will inevitably interfere with the color presentation. Artwork can only be a reliable guide when printed on the physical substrate, with the most common photo paper applied.
You may read here to understand more about how our company ensures color fidelity and consistency for all our orders.
Measures taken to achieve high color fidelity and consistency in reprints
3.2 Excellent Dimension Stability
There is an increasing requirement for the dimension stability of the yogurt bags when the roasters and packers are going to improve the production efficiency with high-speed filling lines. We have quite a good understanding of this and are doing our job to narrow the tolerance of the dimensions for each order produced in our long-term supply. Usually for the 180g yogurt bag, the tolerance should be controlled within +-2%, which can run well on most of the high-speed filling machineries in the market.
3.3 Delicate Bag Making
The bag is achieved with delicate details, which can create a perfect impression for the consumers when they pass by the products, and cause them a purchase. Some customers do like to buy a product out of its gorgeous profile.
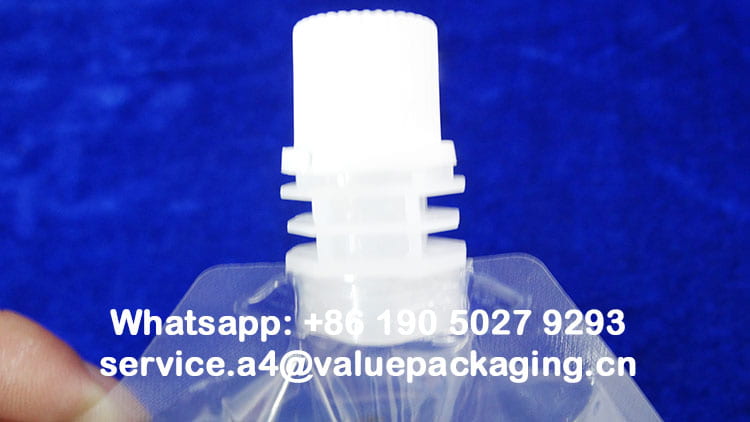
517-clear-standup-pouch-package-for-yoghourt3
3.4 High Barrier Performance
As explained previously, this foil laminate is finalized with a layer of thin aluminum metal sheet, which is of the best barrier performance against oxygen and moisture vapor. Usually, the roasted beans should be well protected to keep the original flavor and fragrance for a prolonged period, to enable the beans enjoyed by the end consumers.
3.5 Fantastic Standup Effect
The bottom of this 180 yogurt bag is much like a box when the yogurt is filled, and that will make the package well stand up on the goods shelf, good for branding and sale.
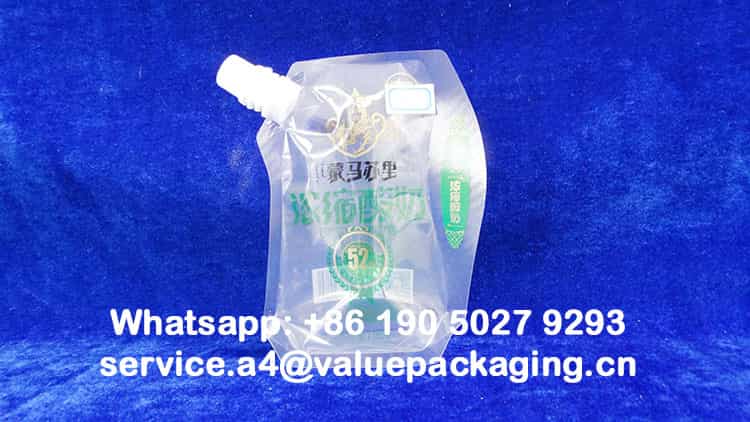
517-clear-standup-pouch-package-for-yoghourt1
3.6 Great Mechanical Strength
This reinforced laminated foil can greatly protect yogurt.
We perform various inspections and tests to check the mechanical strength of the finished pouch, like drop tests, hard sudden strikes, anti-pressure tests
- Tensile Strength
- Sealing Strength
- Anti-puncture Strength
- Burst Impact Strength
- Anti-pressure Property
The above tests are performed against each order, on customer requirements, and you may check the exact values of this foil material PET12/LDPE in the Technical Date Sheet part of this post.
4 Quality Control Measures
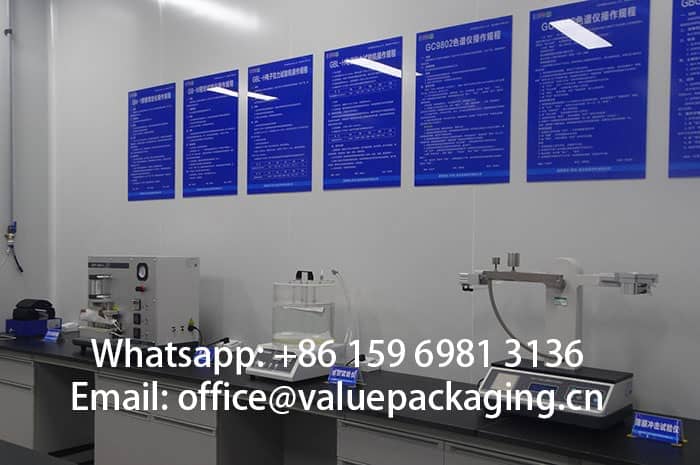
Laboratory-test-equipment
Serious quality control measures have been taken in our manufacturing plant, to ensure each order is finished meeting the requirements of particular customers. With more than ten years of working experience in this field, we finalize this QC manual standard, to make sure each order is produced following the correct procedure.
Here, please allow us to guide you further into our QC system.
4.1 Manufacturing Traceback
We apply a strict recording system to document the manufacturing details, such as environmental conditions, craftsmanship parameters, production facility conditions, etc, which allows us to trace back whenever there is a problem.
4.2 QC Test Report Against Each Order
There will be a QC test report issued against each order produced, with the core items evaluated in it. It is highly appreciated by our customers.
4.3 Print Inspection
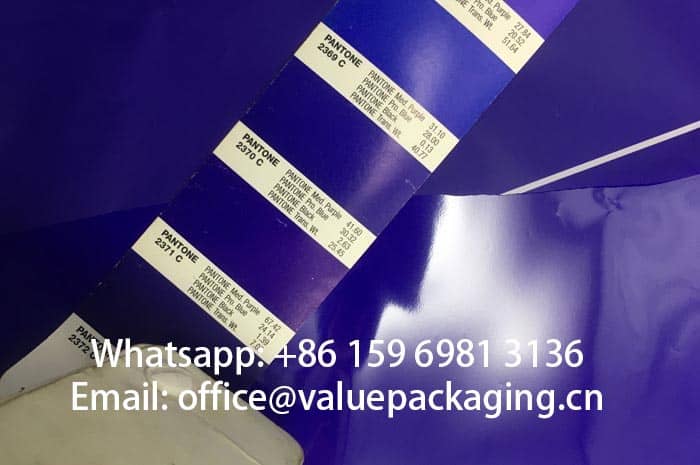
Pantone-color-examine-purple
In our manufacturing plant, the print inspection is always taken and done seriously, as we will never allow the customer’s artwork to be achieved in a way that deteriorates their business. On our gravure print press, there is an in-line inspection system that can eliminate more than 98% of the defects in the printing process.
You may check how it works on our control panel.
There is also a supplementary off-line inspection equipment, to allow us to do the print inspection again whenever it seems necessary.
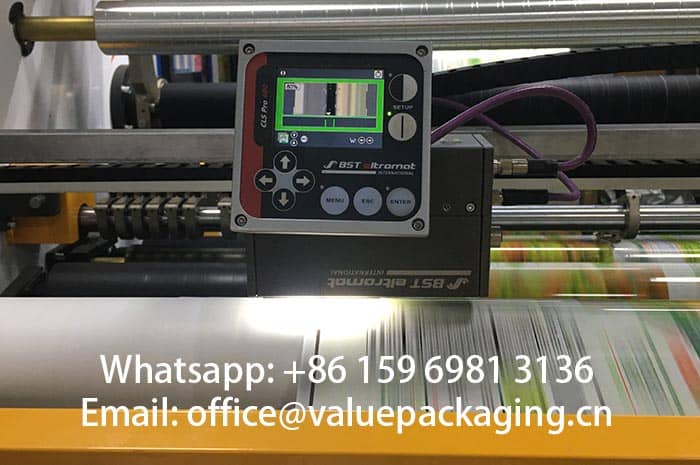
off-line-gravure-print-inspection-for-roll-foils
We are now producing yogurt bags against customer artwork, and we surely love to support the startup and market-testing period for our customers. We will accept a minimum order quantity of 10,000 bags printed against customer artwork design.
4.4 Airtight Property Test
The finished yogurt bag should be completely airtight, to get the products well-protected from oxygen and moisture in the environment. We perform the airtight property test against each order with the device as below.
In actual operation, we will pick up 1 bag every 1,000 pcs, and perform the test following the procedure in our QC manual.
4.5 Drop Test
Drop test should be considered a very reliable way to check if the yogurt bag’s strength is enough to meet the various conditions, as it copies the way when the products fall off the good shelves, and the finished bag will suffer great sudden shock. In our daily QC work, We perform drop test against each order, of course, the standard for this drop test should be decided against customer needs.
Here, we are going to drop the filled yogurt bag from 1.6m high, for 5 times.
You are advised to watch the video below, for a further understanding.
After 5 drops for each bag, none of them breaks, all are fine and dandy.
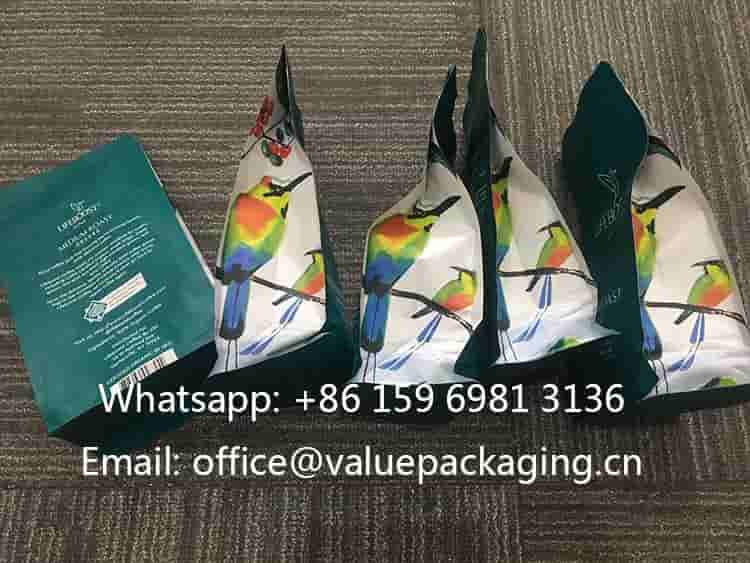
nonbroken-bag-after-drop-test-5times
4.6 Hard Sudden Strikes on inflated bags
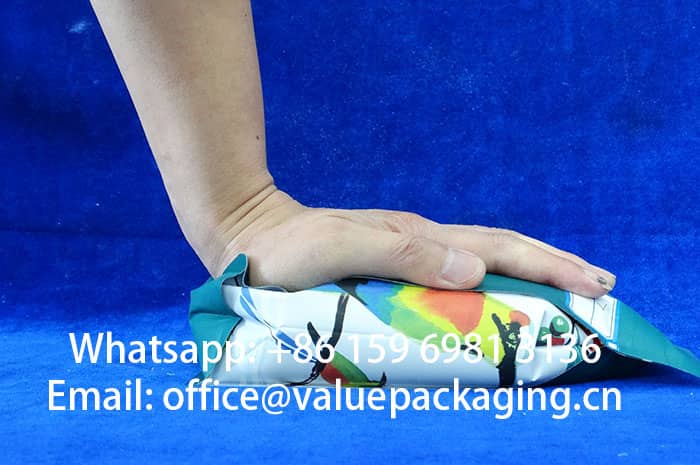
hard-strike-on-inflated-bag
Hard sudden strikes should be taken as a more fierce test method than drop test, as it causes much higher force on inflated packages.
Let’s watch the video to understand how we perform this test in our manufacturing plant.
4.7 Anti-Pressure Test
Pressure-resistance test is another effective method to decide if the final package will serve as great protection for the products, especially liquid products, like household detergent liquids, and windshield washer fluids. For yogurt bags, we will perform the anti-pressure test in our daily QC work, to ensure each order is finished with great mechanical strength.
The leakage or breakage of the yogurt bag will surely be a disaster, either for the distributor or the manufacturer. We will never expect this thing happens in our customer’s business.
Sometimes, for easier and faster operation, we may just get one person to stand on the well-sealed and inflated yogurt bag, to check if there is any burst of them.
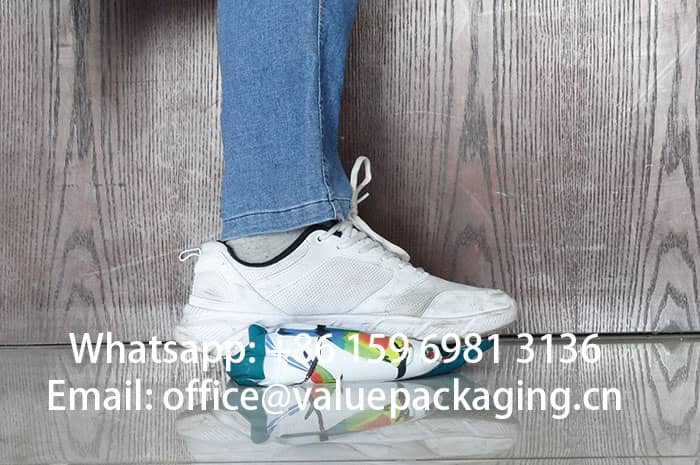
Bruce-standing-on-inflated-bag-package
4.8 Laboratory Tests
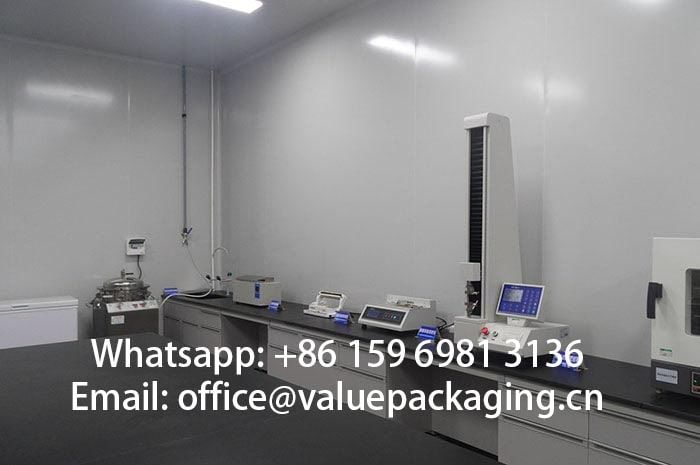
Laboratory-test-equipment-tongli-packaging
Laboratory tests are essential to keep us updated with the intrinsic properties of the foil materials which are not visible to the human eyes. It is crucial to gain a thorough understanding of the data about the production of our bags. The craftsmanship can be improved bit by bit to pursue premium quality bags based on thorough analysis and application of these data. You may check more of these tests in the Technical Data Sheet part of this post.
4.9 Third-party Inspection
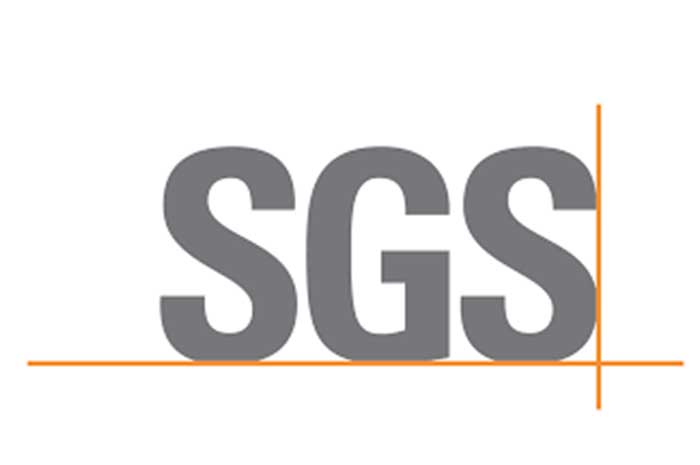
SGS-third-party-inspection
Third-party inspection is available for all our orders on agreed standards or regulations.
5 Human Food Safety
All the film materials, inks, adhesives, and solvents used to convert into kinds of food bags and packaging materials will comply with the regulations for human food safety. The below graphic shows the mass spectra in migration tests on these multilayer flexible pouches that are in direct contact with foods.
Through the below link, you will be able to study the certificates on each of the materials adapted in our factory.
6 Dieline of 180g standup yogurt bag
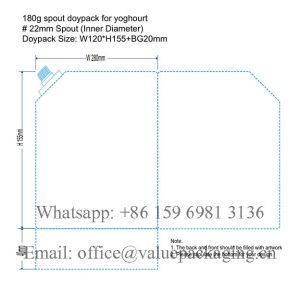
Design Template of 180g Doypack W120XH155+BG20 22mm Spout 517
The die-line of this 180g standup yogurt bag is essential when the customers want to achieve a fantastic artwork design for their package. All the details, like dimension, valve position, and zipper position are well stipulated in this die-cut line.
We attach the editable PDF file here, and the customer can just download and forward it to his designer for further creative work.
Design Template of 180g Doypack W120XH155+BG20 22mm Spout 517
7 Technical Data Sheet of 180g standup yogurt bag

Laboratory-test-flexible-roll-foil
Here, we include the specifications on some main items of this multilayer 180g standup yogurt bag, with the videos showing the test progress in the later columns.
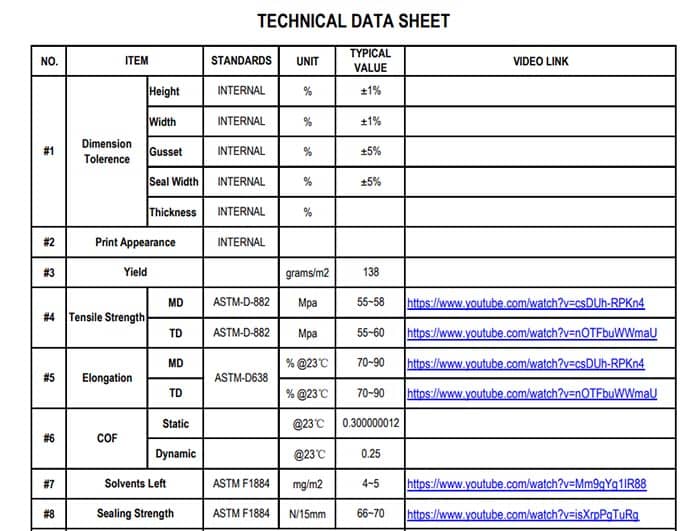
technical-data-specification-sheet-with-test-videos
You may check the attached PDF file for further knowledge on the specifications of this 180g standup yogurt bag.
TL-517 Technical Data Sheet of 180g spout doypack for yogurt
Some main items are listed below.
- Dimension Tolerance
- Print Appearance
- Yield (grams per square meter)
- Tensile Strength (Mpa)
- Elongation Rate (%)
- Coefficient of friction, short as COF
- Solvents Left (mg/m2 )
- Sealing Strength (N/15mm)
- Sealing Conditions
- Bond Strength (N/15mm)
- Burst Strength (J)
- Anti-Puncture ability (N)
- Drop Test Ability (cm)
- Anti-pressure ability (kgs)
- Water Vapor Transmission Rate (g/m2/24hr)
- Oxygen Transmission Rate (cc/m2/24hr)
Just reach us if you have any questions about any of the items.
8 More Sustainable Options
With the increasing burden on plastic pollution, more and more manufacturers are now seeking more sustainable packages, like compostable film materials, recyclable mono materials packages, and plant-based materials packages. They all prove to be more eco-friendly and sustainable than the traditional plastic films which are usually derived from fossil chemicals, and very difficult to recycle and break down in the environment.
Here, we are going to share some of the trending sustainable packages for the yogurt market.
8.1 Compostable film material packages
Thanks to the fast development of plant-based film materials, we can present the multi-layer standup pouch and roll foils in full compostable and biodegradable options.
The compostable substrate films we adapt to convert the multi-layer flexible pouches are listed below.
- BOPLA Film
- PLA+PBAT Film
- Kraft Paper
- Metallized Paper
- Cellulose Film
- Metallized Cellulose Paper
- PBS Film
- PVDC Coated Cellulose Film
- Metalized BOPLA Membrane
We are now achieving multilayer compostable foil materials based on extrusion coating lamination, solvent-free lamination, and dry lamination, and then converting them into various types of flexible pouches against customers’ requirements.
Some of the common compostable foil structures are listed below.
- Kraft Paper/PLA+PBAT Membrane
- Kraft Paper/BOPLA Membrane
- Cellulose/PLA+PBAT Membrane
- Kraft Paper/PBS Foil Membrane
- Metallized Paper/PLA+PBAT Membrane
- BOPLA/PLA+PBAT Membrane
- Cellulose/Metallized Cellulose/PLA+PBAT Membrane
- Kraft Paper/Metallized Cellulose/PLA+PBAT Membrane
- Cellulose/Metallized Paper/PLA+PBAT Membrane
- Kraft Paper/Cellulose/PLA+PBAT Membrane
- Kraft Paper/Cellulose/PBS Membrane
- Metallized Paper/Cellulose/PLA+PBAT Membrane
Here, we are going to introduce the main performance of these compostable materials pouches.
a. Compostable
All the film materials we adopt are certificated compostable, under home or industrial conditions, complying with the standards EN 13432 or ASTM 6400.
The films will present different biodegradation behaviors under different conditions, such as industrial composting facilities, home and garden conditions, and natural soil conditions.
In most cases, industrial composting will be able to achieve faster biodegradation of the compostable film materials than other composting progress, as it can provide better conditions.
Some manufacturers would like to have better biodegradation behaviors of their compostable packages under natural soil conditions, as in most cases, the abandoned package may not be recycled into human composting facilities.
You may read here to have a better understanding of the breakdown progress of our compostable foil laminated materials under the natural conditions in Qingdao, Shandong, North China conditions.
The biodegrading process of compostable film materials buried in nature soil
b. High-barrier performance pouches
Through vacuum metallization, PVDC coating, and AlOx/SiOx depositing, the compostable films can be achieved with better barrier performance, such as water vapor transmission rate (short as WVTR) and Oxygen Transmission Rate (short as OTR). Later on, we will combine several layers of the barrier film and convert it into laminate foil, with an improved barrier property for finished packages. models, or soup products
In the below table, we are going to share some barrier data of the most common foil laminates tested on our Mocon permeation tester.
Biodegradable Foil Laminate | WVTR (g/m2/24hr) | OTR (cc/m2/24hr) |
BOPLA40/PLA+PBAT60 | 62.2 | 267 |
Cellulose30/PLA+PBAT60 | 131.5 | 5.6 |
Kraft Paper45g /PLA+PBAT60 | 44 | 742 |
Kraft Paper45g/BOPLA40 | 41 | 380 |
Metallized Paper69g/PLA+PBAT40 | 27 | 127 |
Cellulose30/Metallized Cellulose20/PLA+PBAT60 | 23 | 0.16 |
Cellulose30/Metallized Cellulose20/BOPLA40 | 25 | 0.12 |
Metallized Paper 69g/Cellulose30/PLA+PBAT60 | 5.6 | 1.12 |
Kraft45g/Metallized Cellulose20/PLA+PBAT60 | 26 | 0.22 |
Cellulose30/Kraft45g/PLA+PBAT60 | 19 | 117.2 |
Cellulose30/Metallized Paper69g/PLA+PBAT60 | 8.9 | 1.1 |
c. Alkaline Resistant
We put a certain amount of bleaching powder into the compostable pouches with various foil structures, and placed them in an environment of 40~45 Celsius degrees, to accelerate the aging process of the compostable pouches.
The test result proves the compostable pouches will be fine for packing alkaline products, like household detergent powder, and hand wash cubes.
However, it is not ok for household liquid detergent and other liquid cleaning chemicals.
You may watch the video below for further knowledge on it.
d. Frozen Treatment
The compostable pouches can be well intended for frozen treatment for some food products, and the mechanical property of the frozen pouch still works well as good protection for the products during the transportation and distribution process.
You may watch the video below to study the test in our office.
d. Vacuum Packages
The compostable pouches can be intended for vacuum packages for products, like milk powder, nutrition products, etc.
f. Hot Filling up to 100 Celsius Degree
The compostable pouch will be fine for the hot filling process, which may work well for juice products.
Watch the video below to learn our test.
g. Microwave Oven Treatment
The compostable doypack can be well intended for microwave oven treatment, such as melting the candle wax, etc.
Please note, that there should not be a metalized film layer in the compostable pouch when it is intended for this microwave treatment purpose.
You may read here for a better understanding on the compostable plant-based film materials packaging.
8.2 Mono Materials Recyclable Pouch Packages

804-matte-black-mono-materials-standup-doypack-with-zipper-coffee-bag-250g
Mono materials pouch packages are truly recyclable, as they can be easily processed into plastic granules which can be used again for other applications. However, for the traditional multilayer laminates, take PET/LDPE for example, it is difficult to process, as PET and LDPE are quite different materials, and can not be melted under the same conditions. That’s why momo materials pouch packages are becoming so widely popular in the packaging field, and highly reputed in the consumer market.
At present, mono-material pouches are divided into Polyethylene channels and Polypropylene channels, with polyethylene channels much more popular, as they can be converted into kinds of standup pouch packages with relatively high performance.
Here we list the film materials that can be well intended for mono-materials recyclable pouch packages.
- MDOPE Film
- BOPE Film
- APE Film
- LDPE Film
- LLDPE Film
- CPE Film
- ABOPP Film
- CPP Film
- VMCPP Film
- VMBOPP Film
- EVOH-LDPE Film
- HDPE Film
Various foil laminates can be achieved based on the above film materials with different properties, which are intended to meet the particular requirements for specific products. Some of the common mono-material foil laminates are listed below.
- MDOPE/APE
- MDOPE/LDPE
- MDOPE/EVOH-LDPE
- MDOPE/HDPE/APE
- MDOPE/BOPE/APE
- BOPE/APE
- BOPP/CPP
- BOPP/VMCPP
- ABOPP/VMCPP
From our experience, mono-material pouches can be well intended for spice powder products.
You may have a further understanding of the recyclable mono materials and pouches here, and just reach us if you have any questions
9 Reliable filling machinery to fill products into this yogurt pouch
Our bags are produced for running on high-speed filling lines, which maximizes production efficiency. Of course, you will have to find a reliable filling machinery to do this job.
Here, we will share with you a reliable filling line to carry on the work of filling yogurt into yogurt bags.
Enjoy!
10 About the manufacturer
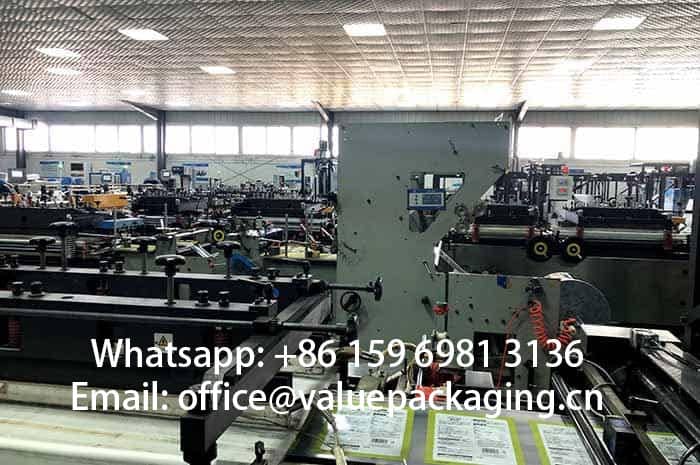
bag-making-department
Qingdao Tongli Packaging has devoted itself to the manufacture of quality yogurt bags for more than 10 years, with long-term customers around the world. You may just rely on us if you would like to get a sustainable and reliable supply of your yogurt packages.
Reviews
There are no reviews yet.